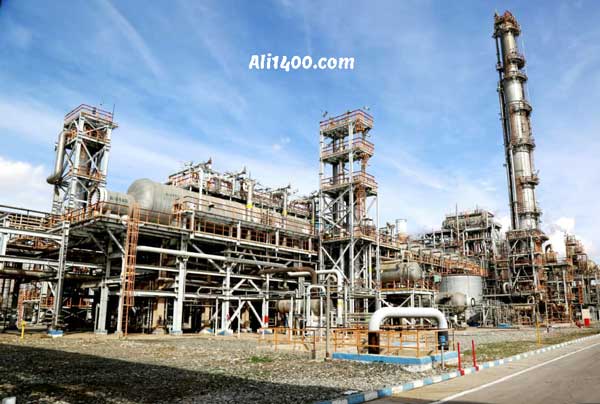
فاز یک مجتمع پتروشیمی اوره و آمونیاک …… در سال 1392 به بهره برداری رسیده و مدیریت شرکت به منظور توسعه مجتمع و نصب و راه اندازی ماشین آلات فاز دوم ، درخواست مبلغ چهار هزار میلیارد تومان تسهیلات را به بانک عامل ارائه داده بود و بانک هم طی ابلاغیه ای ارزیابی قیمت کارشناسی ماشین آلات ، تجهیزات و تاسیسات موجود (فاز یک) را به هیات کارشناسی ارجاع داده که گزارش آن ارزیابی ماشین الات و تاسیسات طی 120 صفحه تهیه و تحویل شد
در ادامه بخشی از مقدمگزارش ارزیابی کارشناسی ماشین آلات پتروشیمی اوره و آمونیاک تقدیم میگردد:
گزارش ارزیابی کارشناسی ماشین آلات پتروشیمی اوره و آمونیاک : شرح فرآیند واحد آمونیاک
طراحی واحد آمونیاک پتروشیمی …… تحت دانش فنی شرکت کلاگ انگلستان M.W.Kellogg میباشد.
این واحد برای تولید 1200 تن در روز آمونیاک و 1494 تن دی اکسید کربن با خوراک گاز طبیعی طراحی شدهاست.
1132 تن در روز آمونیاک گرم با دمای 37 درجه سانتیگراد به واحد اوره ارسال و مابقی با دمای 35- درجه سانتیگراد به مخزن فرستاده میشود.

شرح فرآیند واحد آمونیاک
- آماده سازی گاز سنتز

در این بخش ابتدا گاز طبیعی توسط کمپرسور C-2102 تا فشار 44BARA متراکم شده و پس از پیش گرم شدن تا دمای371درجه سانتیگراد در دستگاه متانیتورMethonotor-R2106 و سولفورزدای Desulphurlse-R2108A/B تحت عملیات گوگردزدایی قرار میگیرد.
خوراک گوگرد زدایی شده با بخار MPS مخلوط شده و وارد لوله های حاوی کاتالیست نیکل میگردد.
این لوله ها در داخل یک کوره (Primary Refurmer ریفورمر اولیه یا H-2101) قرار داشته و واکنشهای زیر انجام میشود:

گرمای موردنیاز برای واکنش از تزریق مشعل های گازسوز داخل کوره تامین میگردد.
بدین ترتیب دمای گاز تا 812 سانتیگراد بالا میرود. برای تکمیل واکنش تولید گاز سنتز، گازهای خروجی به ریفورمر ثانویه Secondary Reformer (R-2102) وارد میشوند در اینجا گاز با هوای فرآیندی مخلوط شده با اکسیژن و محترق میگردد.
بدین ترتیب حین عبور از بستر کاتالیستی موجود در ریفورمر ثانویه دما تا 994 درجه سانتیگراد افزایش مییابد. متان باقیمانده کاملاً به گاز سنتز تبدیل شده و نیتروژن باقیمانده برای تولید آمونیاک فراهم میگردد.
سپس گازها تا دمای 371 درجه سانتیگراد خنک شده وارد راکتورهای شیفت دما بالا (High Temperature Shift Converter-R2104) و دما پائین (Low Temperature Shift Converter-R2109 ) میشوند.
در این مرحله منواکسید کربن با بخار بصورت زیر واکنش میدهد:

2- خالص سازی و تصفیه گاز سنتز
در این بخش گاز سنتز اولیه جهت جداسازی دی اکسید کربن برای بدست آوردن گاز سنتز حاوی هیدروژن و نیتروژن وارد برج جذب (CO2-Absorber-T2101) میشود.
جداسازی دی اکسید کربن با استفاده از منواتانول آمین MEA تحت دانش فنی BASF صورت میپذیرد. سپس دی اکسید کربن و منواکسید کربن باقیمانده در راکتور متانیتور (Methanitor R-2106) به متان تبدیل میگردد.
دی اکسید کربن خروجی از برج دفع (T-2102) مستقیماً به واحد اوره ارسال میشود.
3- تولید آمونیاک
گاز سنتز خالص شده که شامل نسبت مناسبی از هیدروژن و نیتروژن است در کمپرسور گاز سنتز (Synthesis Gas Compressor C-2103) چهار مرحلهای که نیروی محرکه آن توربین بخار HPS میباشد تا فشار 144bara متراکم میگردد. در مرحله آخر تراکم، گاز سنتز با گازهای خروجی از راکتور تولید آمونیاک (Athanolal Converter R-2105) مخلوط میشود.
گازهای خروجی از کمپرسور تا دمای 35- درجه سانتیگراد در یک چیلر چهارمرحله ای خنک میشوند. بدین ترتیب آمونیاک موجود در گاز سرد شده، مایع شده و بعنوان محصول آمونیاک سرد جدا میگردد.
راکتور تولید آمونیاک (Ammonia Refrigerant Compressor-C -2105) یک راکتور افقی حاوی کاتالیست آهن با بستر میباشد که در آن واکنش تولید آمونیاک انجام میپذیرد:


4- سیستم تبرید
سیستم تبرید شامل کمپرسور تبرید (C-2105)، کندانسور آمونیاک (Refrigerant Condenser-E-2127) و دریافت کننده آمونیاک (Refrigerant Receiver D-2109) میباشد.
سیال کاری سیستم آمونیاک بوده و چهار سطح تبرید را ایجاد میکند. این سیستم موظف است تا گاز سنتز را خنک نموده و آمونیاک را از آن جدا کند.
5- سیستم بخار
در واحد آمونیاک عمدتاً بخار از گرمای مازاد فرآیند تولید میشود. یک بویلر کمکی و ریفورمر اولیه نیز در تولید بخار نقش مؤثری دارند.
بخار تولید از نوع بخار فشار بالا (HPS) میباشد که در کمپرسور سنتز و تبرید مصرف و به بخار فشار متوسط (MPS) تبدیل میگردد بخار فشار متوسط (MPS) نیز در توربین های کمپرسور هوا، کمپرسور گاز، کمپرسور واحد اوره و ریفورمر اولیه مصرف میگردد.
قسمتی از آن نیز در سایر توربینها به بخار فشار پایین (LPS) تبدیل و به واحد اوره ارسال میشود.
گزارش ارزیابی کارشناسی ماشین آلات پتروشیمی اوره و آمونیاک : شرح فرآیند واحد اوره
آمونیاک خالص با دمای 37 درجه سانتیگراد و فشار 26 بار از واحد آمونیاک دریافت شده و در پمپ سانتریفوژ چندمرحله ای فشار بالا P-4104 تا فشار 164 تا 170 بار فشرده میشود و بعد از عبور از اجکتور مایع- مایع با همراه کردن RECOVERY سیستم به پول کندانسور E-4103 که یک راکتور افقی و دارای مبدل داخلی برای جذب گرمای حاصل از انجام واکنش میباشد وارد میگردد.
دی اکسید کربن نیز با غلظت حدود 99 درصد حجمی با فشار 1.8bara و دمای 43 درجه از واحد آمونیاک وارد ساکشن کمپرسور چهارمرحله ای شده و تا فشار 144 تا 146 بار فشرده گردیده و پس از ورود به HP STRIPPER (E-4102) همراه کردن قسمتی دیگر از RECOVERY سیستم (گازهای حاصل از تجزیه کاربامات تبدیل نشده به اوره که در E-4104 جذب کاربامات گردیده است) وارد پول کندانسور گردیده و با توزیع یکنواخت در طول راکتور و زمان اقامت مناسب به همراه آمونیاک وارد واکنش میگردد.
واکنش در فشار 140 تا 144 بار انجام میگیرد. در خروجی از پول کندانسور 60 درصد، کل اوره سازی انجام یافت و غلظت در خروجی به 22 درصد میرسد.
سپس مخلوط دو فازی گاز و مایع خروجی وارد راکتور عمودی سینی دار آدیاباتیک شده R-4101 و با طی کردن مسیر نهایتاً غلظت اوره به 34 درصد رسیده و گازهای خروجی با جذب در اسکرابر به ورودی پول کندانسور برگشت داده میشود و مایع خروجی از راکتور وارد HP STRIPPER شده و یک مرحله با انجام فرآیند استریپینگ تغلیظ و سپس با کاهش فشار 138 بار وارد LP SECTION گردیده و با فرآیند EVAPORATION که در E-4106 رخ میدهد و سپس فلش در D-4103 و EVAPORATION تحت خلاء در دو مرحله که به ترتیب در E-4109 و E-4110 به غلظت 95 درصد با دمای 130 تا 133 درجه رسیده و سپس با اضافه کردن اوره فرمالدیید به آن به واحد گرانول ارسال میگردد.
ضمناً گازها و بخارات حاصل از فرآیندهای فوق از طریق LP SECTION و به وسیله E-4107 و D-4105 و سپس P-4107 به صورت کاربامات و مایعات پسماند داخل TK-4108 از طریق سیستم DESORBER که شامل T-4104 و T-4105 و E-4105 به لوپ سنتز برگشت داده میشود.
محلول اوره 96 درصد از طریق P-4109 وارد واحد گرانول و وارد گرانولاتور (V-4208) گردیده و بوسیله هوای اتمایز که از C-4201 وارد نازل های گرانولاتور میگردد انتقال جرم انجام داده و آب محلول اوره وارد هوا گردد و اوره جذب دانه های ریز داخل گرانولاتور میگردد.
سپس دانه های گرانول از گرانولاتور خارج و در داخل کولر اولیه E-4207 از دمای 90 تا 60 درجه خنک گردیده و سپس وارد سیستم سایزبندی OS-4202 گردیده و دانه های خروجی که به سه سایز نرمال، درشت و ریز تقسیم بندی شده اند به ترتیب به E-4208 (کولر نهایی) و HP-4202 (کراشر) و V-4208 (گرانولاتور) هدایت میگردد و محصول نرمال بعد از خروج از کولر نهایی به سیستم توزین WR-4202 هدایت و از آنجا به واحد بالک هدایت میگردد و دانه ریز به همراه محصول خرد شده در داخل کراشر به عنوان هسته اولیه با گرانولاتور برگشت داده میشود


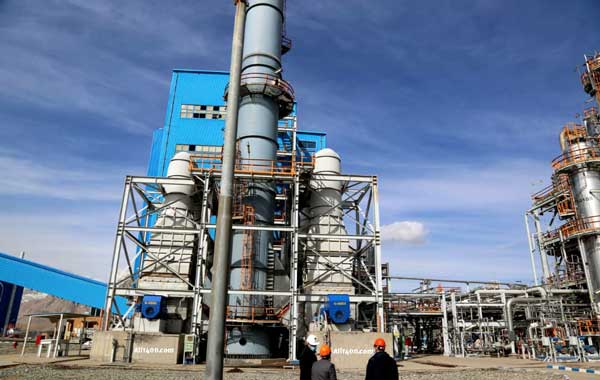
به منظور رعایت موازین امنیتی و حفظ اطلاعات کارفرما ، نام ها از گزارش حذف شده است
پاسخ دهید